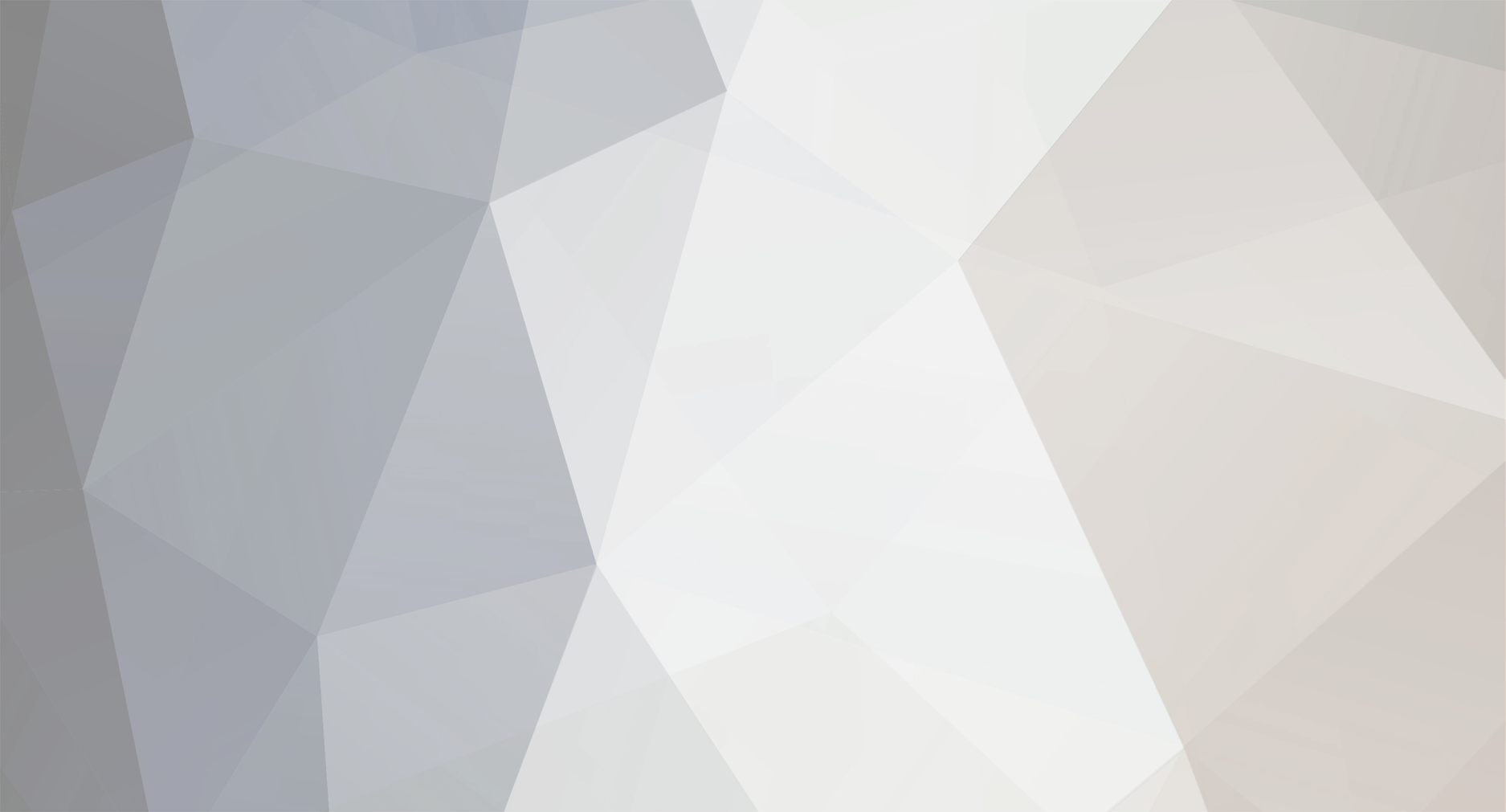
jamesmking
High Rollers-
Posts
406 -
Joined
-
Last visited
-
Days Won
1
jamesmking last won the day on July 27 2021
jamesmking had the most liked content!
Converted
-
Hobbies
breaking 2mm carbide end mills
-
Headphones
stax sr007a
-
Headphone Amps
DIY T2, DIY joamat mini t2, DIY single box blue hawaii se, megatron, DIY hi-amp alpha centauri
-
Sources
garrard 401, loricraft psu+plinth, hadcock 242 se, ortofon cadenza bronze, leema agena, mf v90 dac + golden reference LV psu + synchronous rectifier
-
Other Audio Gear
quad esl 2805, leema hydra, townshend allegri, dcs 905 adc, ps audio p3, van den hul first cables, cardas golden reference mains cables, cardas golden reference speaker cable
Recent Profile Visitors
The recent visitors block is disabled and is not being shown to other users.
jamesmking's Achievements

Limited Edition Bronze Participant (4/6)
592
Reputation
-
goldenreference high voltage power supply (GRHV)
jamesmking replied to Pars's topic in Do It Yourself
for my megatron build (which uses a 300V golden reference hv psu rail) I used 250VAC which gives peaks of about 350V with nominal AC mains voltage. -
be careful, the ssth512 has an insulated body and no live tab. The DSEP12-12 has a live metal tab and will have very high voltages on it.
-
the problems with the stax srm006t is that like the srm007 it has too many design compromises that massively effect the sound. 1. its high voltages are not well regulated 2. it uses resistors as a anode load for the valves which reduces current drive and efficiency rather than using a constant current source. (the srm007t is exactly the same design but parallels up the values to get a bit more drive but its still not fixing the problem and costs twice as much) 3. it uses values which don't have much current drive or are that high voltage. Most of the good designs use far more powerful values such as EL34 running at conservative currents (for what they can do) rather than running tubes design for pre amps really hard. The result of this poor bass, poor dynamics, mushy and in general, a sound that, as you turn the volume up the bass gets more soggy but not that much louder. The drive situation gets far worse if you use a difficult to drive headphone like the sr007 (I tried this and you cant get even close to the performance the 007s can provide with a well designed energizer. Replacing a silicon diode bridge with Schottky diodes might give you a bit less switching noise and slightly lower voltage loss but its not addressing the major design issues. If you really want to upgrade the energizer get the anode resistors replaced with a constant current source. This massively increases the drive and addresses some of the poor design of the energizer. If you are in to diy electronics and want to build your own energizer there are a variety of energizers so much better than the srm006 or srm007. one of the simple and fairly cheap options, with better valves and fully regulated high voltage power supplies is the alpha centauri from http://www.high-amp.de. Its relatively simple to build and walks over and kicks in the head the srm006t. I am speaking from experience here. I started with a 006 and built the centauri. The published design still uses resistors for the anode load but the website does offer pre built constant current sources for it. Unfortunately the schematics and the pcb files are not available for the constant current sources. Next come the energizers with constant current anode sources, fully regulated high voltages and beefy output valves: The blue hawai, it will cost more to build than the alpha centauri, is bigger and more complex but sounds even better At the apex of stax energizers is the diy T2. The original one uses transistors which are no longer available and so getting non fake transistors for it is not easy or cheap. The design has been updated to use more modern transistors. I built the mostly modern version which has a mix of old and current production transistors. It big, complex and fairly expensive to build but the performance is fantastic. I replaced by blue hawaii with it and never went back. There is also a mini T2 which is a simplified version using modern transistors and smd (surface mount components). Its not as good as the full T2 but I think its better than the blue hawaii. if you want something that is fairly simple and will warm up a room on cold nights then there is the megatron. I never got around to finishing my build but its one of the more simple designs. There are many more diy designs out there and in this forum. But the bottom line is if you want a realy good energizer for your Stax headphones, Stax does not sell one and most of the other commercial designs are almost equally as bad (and in some cases worse). P.S. the offset or balance DC voltages being a few volts out or drifting around by a few volts is not going to effect the sound or reliability. Remember the headphones are designed to take 100s of volts, 5V or 10V of DC offset or DC balance is nothing to them.
-
Megatron Electrostatic Headphone Amplifier
jamesmking replied to kevin gilmore's topic in Do It Yourself
22ohm to ground on the heater/filament looks like its there to stop the heater floating and might reduce hum and is therefore probably optional. It looks like this resistor is not present in the megatronpowersupply300v2xl gerbers. It also looks like there is a 221 ohm resistor between the anode and G2 of the el84 in the gerbers which is not present in the megatronps300.pdf. I am afraid I did not build this power supply so I can't comment on which is the more up to date or preferred version. But in general its the Gerbers which people get pcbs made from and therefore is assumed to be correctly functioning unless the threads on headcase say otherwise. -
you might want to try stereo: Gunter Wand;Ndr Symphony Orchestra (specialist in Germanic symphonies c.f brahms, bruckner) herbert blomstedt;Gewandhausorchester Leipzig Staatskapelle Dresden;herbert blomstedt André Cluytens;Berliner Philharmoniker igor Markevitch;Orchestre des Concerts Lamoureux mono: erich kleiber;vienna po (dad of carlos kleiber) felix Weingartner;london so (first complete recorded beethoven symphony cycle) paul van kempen;berlin po (conductor of kempff classic 1950s beethoven piano concerto cycle) The marmite option: if you like "period instruments historically informed": roger norrington;london classical players
-
Electrolytic caps are well known for being relatively fragile. Almost any reverse polarity voltage will damage them over time. They also degrade with temperature and time too. The input caps take the highest hammering because of the higher input AC voltage peaks compared to the output caps - (which only have to handle well regulated DC). Check if the diodes in the bridge rectifier are leaking, if one of the diodes starts to leak more than a couple of volts that would degrade your input cap. Also, when you have got the amp up and running again it might be worth monitoring the temperatures close to the caps, a rough rule of thumb is every 10C degrees rise in temperature halves the cap life. I have had good reliability experiences with kemet al10 series caps - although they can be expensive they are rated at around 15000 hours at 85C - significantly higher life expectancy than your caps and life expectancy. Part number ALC10A681EL550 is 550V 680uF. The ripple current of the kemet is 50% higher than your caps, but the esr of the kemets is higher, leakage current is the same. Unfortunately kemets tend to go in and out of stock again and the pricing can also be somewhat erratic. note the ALc10 kemets tend to be tall rather than wide - the ALC10A681EL550 is 80mm tall and so you would have trouble fitting it into a 2U high case.
-
farnell in the uk has plenty of stock of the FJPF2145 https://uk.farnell.com/onsemi/fjpf2145tu/trans-npn-800v-5a-125deg-c-40w/dp/3368628
-
FJPF5027OTU seems to be a possibility, seems to have similar specs except lower current rating and the same pinout. Hfe of FJPF2145 is 20 - 40 which is the same as the O variant of the 5027
-
CNC metal machinists (for Stax amp cases) unite?
jamesmking replied to jamesmking's topic in Do It Yourself
-
CNC metal machinists (for Stax amp cases) unite?
jamesmking replied to jamesmking's topic in Do It Yourself
Diamond drag engraving is surprisingly fun and easy. I decided to buy a spring loaded diamond drag engraver and do some experimentation on feeds, cutting depth, stepover etc. I ended up. 90 degree drag bit. tip flat estimated at 0.128mm, 0.1mm step over, fill crosshatch at 0 degree, 700mm/min feed speed. Far better results than using a V bit, much less sensitive to the material not being totally flat and far far faster. -
Well spotted! I didn't notice they are not using the 10Hz standard. I wonder why are they using 100Hz?
-
well specifically, The Denon cart user manual talks about the included headshell will provide the appropriate overhang - well thats BS because there is no standard. They may be referring to SME arms with bayonet fitting. The vinyl engine has specs for the technics arm geometry and its NOT the same as the sme bayonet geometry on say a SME 3009. The effective length, offset angle and overhang are all different, and in fact the sl1700 mk2 has a different offset angle from the mk 1 and therefore different zero tracking error points on the record. The cartridge could be used with the existing technics headshell. The user manual only specifies the weight of the cart and headshell which is not helpful in working out the resonance frequency if the technics headshell is used. The frequency response spec in the user manual does not include + or - dBs and so is meaningless and there are no specs on tracking ability either. There is some information about the diamond BUT nothing on the effective moving mass. the spec sheet contains even fewer specs than the user manual (omitting any information about the diamond)... Finally buried in the Denon blurb in spec sheet is says the headshell is 6g so the cart is 12.5g the suspension is 5*10*-3m/N which is very stiff, but then the cart is quite heavy. The technics service manual says the arm is effective mass 22g so with the technics shell you are looking at a resonance of about 10Hz ish which is ok. According to the technics manual, the arm can ballance carts up to 11g with the technics headshell and the denon is 12.5 so you will need to use a lighter headshell or add extra weight to the back of the arm.
-
oops In my day job I usually lecture to 18+ audience and if no one gives me a limitation on detail I tend to go for high levels of detail because in reality its almost never as simple as X is better than Y, it's almost always the case X and Y offer different compromises and its (in my opinion) important to understand what is going on and understand the compromises.
-
Ok i will open the can of worms. Please note I have had to make a LOT of generalisations here: records are cut with a linear tracking arm and ideally should be played back the same way so the play back diamond is aligned with the cutting diamond. In reality quality linear tracking arms are not easy to engineer and tend to be expensive and so arms that track in an semi-circular arc often used because they can be easier and cheaper to make. But this introduces errors between the alignment of the cutting diamond and the semi circular arc of the playback. you would expect the semi corcular playback arc to only align with the cutting arm at one point. But by some clever geometry it is possible to align two points and reduce the tracking error. If the two zero error points are too close together you get more distortion at the beginning and end of a record then optimal and less distortion in the middle of the record. If the two zero points are too far apart you get lower distortion and the beginning and end but more distortion in the middle. Given different records have different amounts of the record with music on there has always been arguments about the exact placement of the two zero tracking points. Unfortunately to do this trick it requires the cartridge to be skewed compared to the pivot in the arm AND requires the cartridge to overhang the centre point of the record by an amount. This is made more complicated because not all arms have the same pivot to cartridge mounting hole distance and not all cartridges have the same distance from diamond to the mounting holes either. The result is that the diamond to arm pivot distance is not standardised at all. As a result the cartridge has to be moved forward or back in the headshell and/or the base of the arm moved to get the correct overhand from the diamond to the centre of the record. There are various ways of attempting to make this alignment, Some rely on the cartridge being exactly parallel to the headshell and assume the headshell is correctly angled and then slide the arm base or cartridge back and forth until the diamond overgangs the centre spindle by the correct ammount Others methods assume the overhang is correct and have parallel lines at the two zero tracking error points and ask you to adjust the angle of the cartridge in the headshell to be parallel to the lines. A few advanced (and generally expensive) alignment tools actually allow both overhang and angle to be set. However, all this assumes that the diamond is at 90 degrees to the cantilever and the cantilever is parallel to the cartridge etc. In theory proper alignment would be done looking at the diamond rather than the cartridge body. another issue is that the suspension on the cartridge acts like a spring and will resonate at a certain frequency, the higher the mass of the arm + cartridge the lower the resonance frequency. The more stiff the suspension the higher the resonance frequency. If the resonance frequency is too low i.e. the mass of the arm and cart too high and the suspension of the cart too soft then the resonance can be excited by record warps and the suspension can resonate like crazy and even bounce the stylus out of the grove! If the suspension of the cart is too stiff and the mass of the arm and cart to low the resonance frequency can be so high low frequencies in the groves can excite the resonance and cause the suspension to go crazy. This is another reason low mass carts usually have soft suspension and high mass carts usually have stiff suspension. This means some arm and cartridge weight combinations simply will not work well. There are online calculators where you can enter the moving mass of the arm, the mass of the cart and its suspension stiffness and get out the resonance frequency. Similarly some cartridge mounting hole to diamond lengths are outside the adjustment range of some arms or headshells and so it's impossible to get them reasonably aligned - when you decide what reasonably aligned is. Similarly some carts are too light or too heavy for the arm to balance correctly and you either have to add weights to the headshell in the case of too light weight which has the side effect of changing the moving mass and therefore the resonance frequency or add mass to the back of the arm if the cart is too heavy (which will also change the resonance frequency) In other words there are a whole set of interrelated compromises and assumptions about cart mass and suspension stiffness and diamond to mounting hole distance. MC vs MM moving coils generally have a much lower output voltage than moving magnet but a much lower output impedance. A quality step up transformer designed for the job into a mm preamp input is certainly an option. In my experience step up transformers are sensitive to external magnetic fields so try to keep it away from power supply transformers, mains wiring etc. Your Denon MC has 0.25mV and MM carts somewhere around 2mV. So about a x10 step-up or 20dB gain. Generally dedicated Mc preamps will boost to line level ~1.5V or around x1000 or 80dB gain and do the RIAA equalisation and feed into a line level input on the preamp. Low noise MC preamps are a bit of a challenge given the gain they have to do. In general dedicated MC preamps have multiple resistance loading options, many have multiple gain options and some even have capacitance options to. i.e. more scope for tweaking the sound. Is it worth going MC? much more difficult question to answer In general MC are better sounding than MM for a variety of reasons. MM are usually the lower cost option and more design and precision goes into the MC carts which are perceived as the premium cost option. In general MC have lower moving mass because the diamond is attached to a cantilever which is attached to some lightweight coils and the magnets can be relatively large and fixed to the cart body. MM can have lots of coils fixed to the cart body but the magnet is attached to the cantilever and is generally quite high mass. Its that mass the diamond is trying to move when it reads the record grove. MCs generally have better profiled diamonds too which can read more of the fine wiggles in the grove than a cheap profile like a spherical diamond. better diamond profiles will also reduce record wear because the tracking weight is distributed over a taller slice of the grove. MM carts are usually lower mass and so can have a more compliant and soft suspension which in general helps with low frequency tracking performance, but generally have less refined diamond profiles resulting in poorer high frequency tracking but as a result are cheaper to manufacture. MCs usually have better diamond profiles and this helps with high frequency tracking performance but are heavier and so have less compliant suspension and poorer low frequency tracking and since making diamond profiles is precision engineering this makes MC carts more expensive. Because of the higher stiffness/lower compliance of the suspension of the MC cartridge they generally require higher tracking weights to keep them in the grove, conversely MM carts usually require less weight. MM around 1.5Grams MC around 2.5grams. Too little tracking weight and the diamond stops following the grove properly and as well as creating more distortion this can damage the record. So there is a tradeoff too high tracking force and you add to diamond wear and record wear, too little tracking force and your diamond starts to cut its own path through the record groove. Against all of this you have to bear in mind if you wear out the diamond or damage the cantilever, many MM carts have user replicable diamond and cantilever and the diamond profiles are usually cheaper so the running costs are lower and you can keep a spare stylus around for a quick swap out if needed. Some MMs even have a range of available diamond profiles so you can upgrade the performance by replacing the diamond/ cantilever with a higher end one e.g. ortofon om series MM carts. Very few MC carts have user replaceable diamond/cantilevers and so almost all require a rebuild if damaged or the diamond is worn - so the running costs of MC carts are generally higher, in many cases a single rebuild of a MC can be a significant percentage of the cost of simply buying the cartridge again. ( I hope this is not too rambly for you) 😁 please note I have had to make a LOT of generalisations here. There are some high end expensive MM carts with nice diamond profiles and some low end MCs with plastic bodies, low weight and with crappy diamonds (e.g. ortofon mc10 super). Some MC carts can have a high output voltage and some MMs can have a low output voltage (e.g. some grado MMs). etc etc.
-
bit of both. working distance is ok for either a hot air handle or a soldering iron. It takes some getting used to since you have a fixed defined viewing circle, you can't move your head and have to organise everything around that. I personally found that exact head positioning was very critical to get a good 3d perspective view and this meant I wanted to minimise the number of times I looked up away from the microscope.